Maintenance of generators in working condition is undoubtedly important for ensuring a reliable power supply. The central element in this complex system acts as a stator, which is responsible for a stable functionality generator. Stator — this stationary part generator, containing windings, creates necessary magnetic fields for operation. Any damaged stator can lead to serious failures, resulting in a stoppage of the whole generator. Therefore, timely detection of stators and generator repair and service has become a priority for specialists in the field of energy.
Page Content
Critical Role Stator in Reliability Generators
Understanding causes damage stator critically important for preventing breakdowns. This process requires deep knowledge of the subject and a careful approach. The main causes of damage include:
- Overheating: Excessive temperature due to insufficient ventilation, excessive load, or improperly functioning cooling system leads to the destruction of insulation windings and possible short circuits.
- Mechanical damage: Vibrations and impacts during operation can cause deformations or cracks. These damages disrupt the structure and safety generator.
- Corrosion: Metallic parts stators are susceptible to corrosion due to moisture and aggressive environments, especially when equipment is operated in conditions of high humidity or near sea objects.
- Electrical overloads: Excessive loads lead to overheating windings and destruction of insulation, which, in turn, causes short circuits.
Main Causes Damage Stator and Their Consequences
Modern methods and technologies diagnostics are key to extending the lifespan of generator equipment. Among the most effective methods can highlight:
- Visual inspection: Initial stage of any diagnostic process — this thorough inspection for visible damages, such as cracks, discoloration insulation, or traces of corrosion.
- Infrared thermography: This method identifies areas overheating, confirming or rejecting existing problems with cooling or electrical overloads by visualizing temperature distribution.
- Tests on resistance insulation: Allow assessment integrity insulation and identify potential places breakdown at an early stage.
- Analysis vibrations: Identifies mechanical malfunctions, such as imbalance or uneven distribution of mass inside the stator, which can lead to serious damages.
Advanced Methods Diagnostics for Effective Maintenance
Repair malfunctions stator consists of complex stages and requires great attention to detail. Main stages include:
- Dismantling: Organized and safe dismantling generator for subsequent conducting repair works.
- Cleaning: Removal of all contaminants and corrosion from the surface using chemical or mechanical methods.
- Replacement damaged elements: After detailed inspection all damaged components replaced with new.
- Assembly and testing: Assembly equipment and testing for functionality and reliability for preventing future failures.
Stages Comprehensive Repair Damage Stator
Modern innovations significantly increased the efficiency of repair works. New composite materials possess high resistance to corrosion and mechanical loads, which significantly extends the lifespan stator. The application of robotic systems for repair allows for minimizing human errors and increased accuracy of work.
Innovations in Repair: Modern Technologies and Materials
A Common example of successful repair is the application of infrared thermography for identifying problematic zones. For example, at one industrial enterprise located near sea borders, generators often failed due to corrosion and overheating. Using infrared thermography, specialists are able to quickly identify and eliminate problematic areas, which allows enterprises to reduce time on repair and save significant funds.
Successful Cases and Examples Practical Solutions
Investments in regular technical maintenance and diagnostics problems with equipment directly affect the prevention of critical failures in operation generators. The application of advanced diagnostic methods and innovative technologies allows for improved reliability of generator installations and minimizes risk stoppages, which ultimately leads to significant economic benefits for enterprises.
Continuous Technical Maintenance as Main Factor Reliability
Overall, effective technical maintenance generators require deep analysis of causes, modern methods of diagnostics, and variability repair of damaged stators. The application of advanced technologies, materials, and experienced specialists allows for the achievement of high standards in ensuring reliable equipment and extending its operational lifespan.
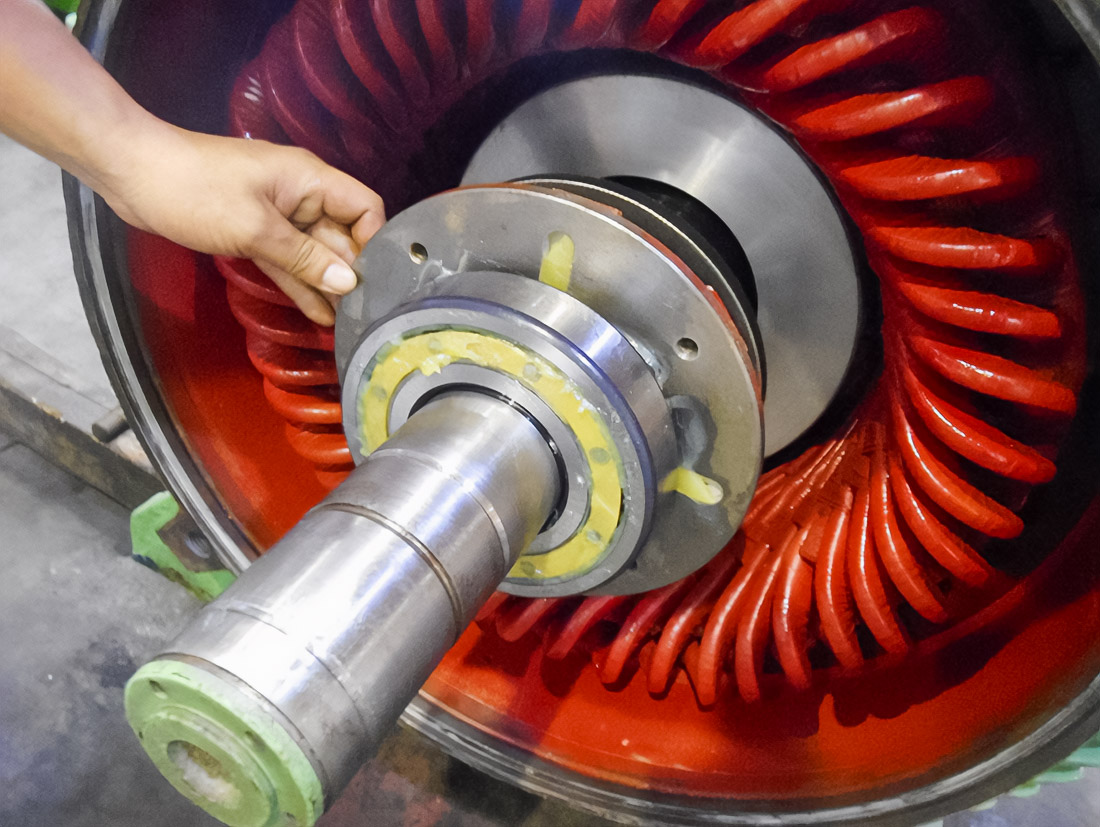